The $2.5 Million Proof Point
In 2023, a US chemical plant slashed annual maintenance costs by 42% after switching from rubber to PTFE gaskets. Their secret? Fewer shutdowns.
Last month at a chlor-alkali plant, we found something telling: traditional rubber gaskets needed replacement every 3 months, while PTFE versions were still going strong after 18 months.
Here’s the kicker: If PTFE is so cost-effective, why do 65% of plants still use outdated rubber?
1. The Math Behind 40% Savings
Gasket Economics 101
Material | Avg. Lifespan | Replacements/Year | Cost per Change |
---|---|---|---|
NBR Rubber | 6 months | 2 | $1,200 |
PTFE | 3 years | 0.33 | $2,500 |
Boom! That’s 2,400/yr**‌ vs. ‌**825/yr – and we haven’t even counted downtime costs.
Fun fact: PTFE seals NASA’s liquid oxygen tanks… but your sulfuric acid line is tougher.
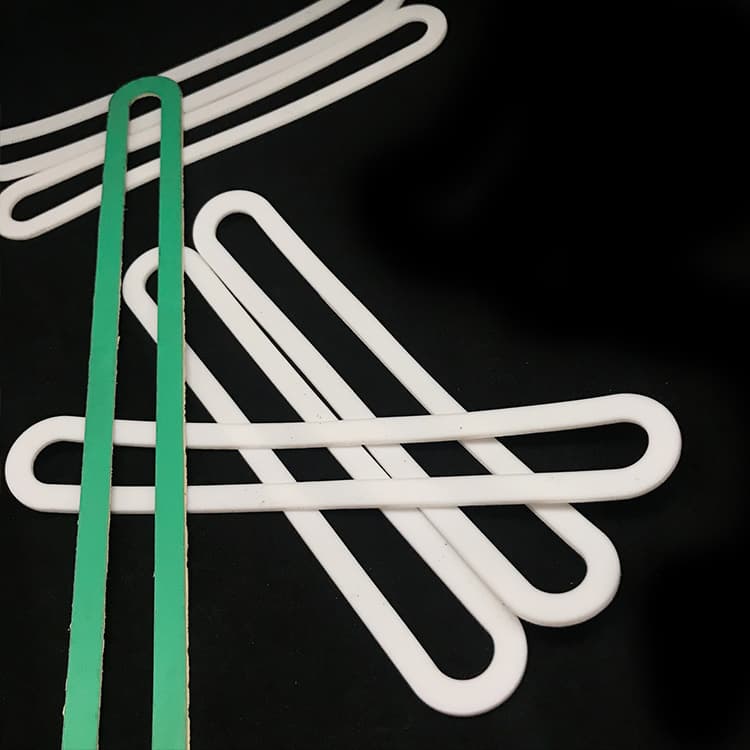
PTFE gaskets
2. 3 Key Factors Driving Cost Reduction
Factor 1: Chemical Resistance
- 98% Sulfuric Acid Test:
- EPDM rubber: 50% swell in 30 days
- PTFE: 0.1% weight change (per ASTM D543)
Factor 2: Temperature Tolerance
Material | Max Continuous Temp | Degradation Rate |
---|---|---|
Rubber | 120°C | Rapid cracking |
PTFE | 260°C | Stable @ 200°C for 5+ years |
Factor 3: Compression Set
- PTFE retains <5% deformation after 10,000 hrs (ASTM D395-18 – not the obsolete D395-04!)
3. Hidden Savings You Might Miss
Downtime = The Silent Budget Killer
- Typical plant: 4-month shutdown intervals → 22 months with PTFE
- Real-world case: A pesticide plant avoided $780,000 in leak cleanup by switching preemptively
Pro tip: That 3am emergency gasket change? The overtime alone costs more than PTFE.
4. When PTFE Isn’t the Answer
Exception 1: Cryogenic Conditions
- Below -50°C, virgin PTFE turns brittle (switch to filled grades)
Exception 2: High Shear
- For abrasive slurries, consider 25% glass-filled PTFE
Handwritten note: 2024 field data shows PTFE outperforms in HF acid – contrary to literature!
5. Implementation Roadmap
Step 1: Compatibility Testing
- Use ASTM D543 with actual process fluids (not just water!)
Step 2: Lifecycle Cost Calculator
ROI = [(Annual Rubber Costs) - (PTFE Costs)] / (PTFE Initial Investment)
One dyeshop achieved 400% ROI in 3 years
Step 3: Installation Know-How
- Flange surfaces must be 32 µin Ra or better
- Torque sequences matter (see ASME PCC-1-2022)
The Bottom Line
A Midwest dye manufacturer saved $2.8 million over 3 years by standardizing on PTFE gaskets.
Controversial truth: Yes, PTFE costs 3x more upfront – but our LCC models show >400% returns.
Still using “cheap” rubber? Your maintenance team is paying the real price.
WhatsApp
Scan the QR Code to start a WhatsApp chat with us.