NBR rubber gaskets have excellent wear resistance. This is due to the introduction of polar cyano groups in nitrile rubber. They improve its structural stability. Also, high-polymerized nitrile rubber has a high crosslinking density. This increases its tensile stress at a given elongation. Reinforcement treatment improves the physical and mechanical properties of nitrile rubber. It boosts its wear resistance and extends its service life.
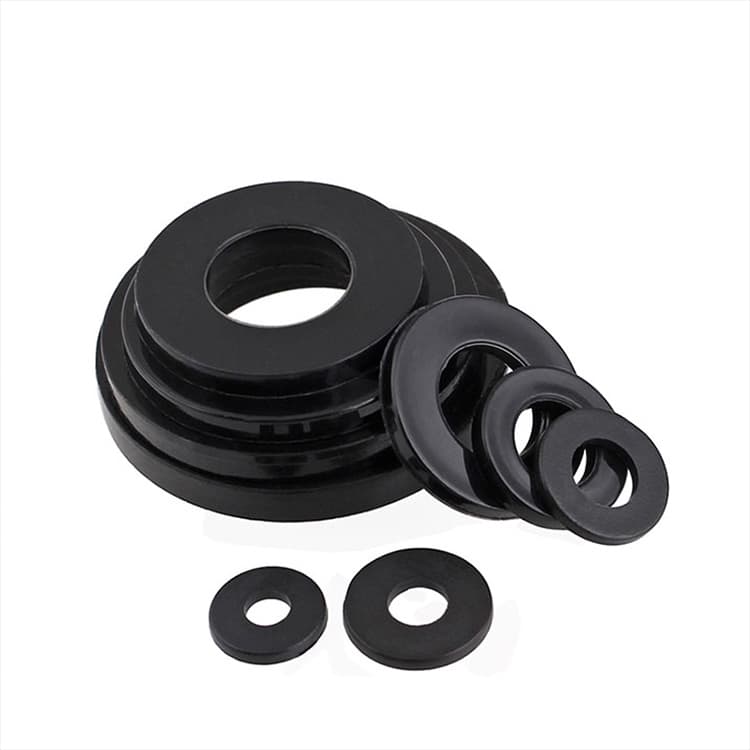
NBR Sealing Rubber Gasket
Nitrile rubber gaskets have outstanding oil resistance. This characteristic sets them apart from many other rubbers. They rank below polysulfide, acrylate, and fluorine rubbers. Nitrile rubber works well with epoxy resin. Manufacturers can make it into rubber-resin structural adhesives. These adhesives have high oil and flex resistance and strong bonds. The automotive industry widely uses this material. Engineers use it for bonding oil-resistant parts and sponge material. It makes oil-resistant hoses, tapes, rubber diaphragms, and large oil bladders.
Nitrile rubber gaskets have excellent heat resistance. Under normal use, users can achieve a heat resistance of 100°C – 120°C. They can continuously operate for 60 days. Especially, hydrogenated nitrile rubber. It can withstand temperatures up to 150°C. This heat resistance makes nitrile rubber popular in the petroleum, automotive, and aviation industries.
A significant advantage of nitrile rubber gaskets is their excellent elasticity. Their good elasticity comes from the absence of sulfur in their formula. This makes the manufacturing process simpler. Also, these gaskets can deform under compression. This lets them adapt to various applications. They resist animal and vegetable oils. Neutral chemicals, fats, and solvents won’t affect their properties.
WhatsApp
Scan the QR Code to start a WhatsApp chat with us.