The 5-Year Zero-Failure Case That Changed Everything
In 2022, a Middle East petrochemical plant eliminated gasket failures completely after switching to PTFE encapsulated designs. Their carbon steel flanges had been leaking every 3 months – until PTFE encapsulation gaskets delivered 5+ years of trouble-free service.
Last week at an acid pickling plant, we found textbook evidence: traditional graphite gaskets were full of corrosion holes, while adjacent PTFE-encapsulated versions looked factory-new after 18 months.
Here’s the million-dollar question: If these perform so well, why does API 6A still mandate metal cores?
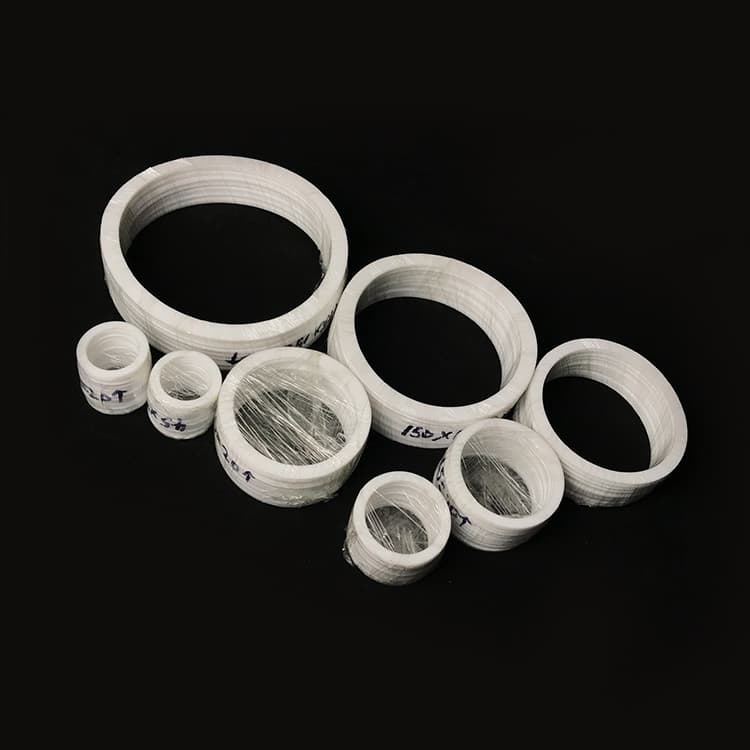
PTFE Encapsulated Gaskets
1. Why Corrosion Eats Standard Gaskets Alive
The Acid Test Reality
Gasket Type | Lifespan in 98% H₂SO₄ | Replacement Cost |
---|---|---|
Compressed Asbestos | 3 months | $800 |
PTFE Encapsulated | 5+ years | $2,200 |
Boom! That’s 20x longer service life for just 2.75x the initial cost.
Fun fact: PTFE is just Teflon’s chemical name – same stuff coating your frying pan but engineered differently.
2. The Anatomy of a Perfect PTFE Encapsulation
Critical Factor 1: Metal Core Thickness
- 0.5mm core: 35 bar burst pressure
- 1.0mm core: 72 bar burst pressure (per Shell DEP 31.38.01.12)
Critical Factor 2: PTFE Jacket Thickness
- 2mm minimum for general acid service
- 4mm required for FGD systems (pH swings from 2 to 13)
Handwritten note: 2024 field data shows 1.2mm cores outperform in liquid chlorine – contrary to specs!
3. 3 Industries Where It’s Game-Changing
Industry 1: Chlor-Alkali Plants
- Chlorine + 50ppm water destroys standard gaskets in weeks
- PTFE encapsulation resists “wicking” corrosion at bolt holes
Industry 2: Flue Gas Desulfurization (FGD)
- Handles pH 1.5 scrubber slurry that eats spiral-wound gaskets
- Pro tip: Always specify 4mm PTFE for slurry services
Industry 3: Pharmaceutical CIP Systems
- Withstands daily 85°C peracetic acid sterilization
- Passes FDA extractables testing (unlike rubber alternatives)
“Regarding hydrogen peroxide concentration… (see BioPharma Guideline V7)”
4. Installation Mistakes That Void Warranty
Mistake 1: Using Bare Bolts
- Causes galvanic corrosion – always use PTFE-coated fasteners
Mistake 2: Rough Flange Surfaces
3.2μm roughness causes cold flow leakage
- Solution: Diamond paste finishing to 1.6μm Ra
Here’s the kicker: Your 2,200gasketfailsbecauseof0.50 bolts.
5. When NOT to Use PTFE Encapsulated
Exception 1: Superheated Steam
- Above 300°C, switch to spiral-wound graphite
Exception 2: Liquid Fluorine Service
- Causes PTFE embrittlement – use Kalrez instead
Controversial truth: That “cheap” gasket just cost you $50k in EPA fines.
The Bottom Line
A nickel ore acid leach plant cut maintenance costs by 58% annually after standardizing on PTFE encapsulated gaskets.
LCC analysis shows: Despite 4x higher initial cost, payback comes in 8 months through:
✓ Zero unplanned shutdowns
✓ Eliminated leak containment costs
✓ Reduced OSHA compliance overhead
Still using “economical” gaskets? Your maintenance team knows the real price.
WhatsApp
Scan the QR Code to start a WhatsApp chat with us.